By Chung C. Fu, Ph.D., P.E.
The Bridge Engineering Software and Technology (BEST) Center
University of Maryland
Bridges are important links of the whole highway system. The most vulnerable element of a bridge is its deck. Bridge deck deterioration of older bridges is a significant problem in aging of the highway system. Every ten to fifteen years, bridge decks have to be replaced. The most common problem of aged concrete bridge decks is the spalling caused by a chain of actions within the deck: (1) melted snow and deicing salt solutions seeping deep into the concrete deck surfaces, (2) chemical reactions with the rebars and (3) an attendant volume increase of the rebars, and (4) a buildup of internal pressure causing material stresses that lead to (5) spalling of the concrete.
Use of FRP-composite bridge decks is viewed as a potential long-term solution for the concrete deck deterioration problem. Other incentives for using FRP-composite materials include the material’s inherent high strength-to-weight ratio. Use of composite structural deck surfaces can decrease the “dead load” associated with the bridge and therefore increase vehicle-load-carrying capabilities of the bridge.
To avoid a costly bridge replacement project in the future, a pilot project was undertaken by the Maryland State Department of Transportation, partnered with the BEST Center of the University of Maryland and sponsored by the Federal Highway Administration (FHWA), to rehabilitate a steel truss bridge (MD24 over Deer Creek) using lightweight FRP deck. Figure 1 demonstrates the lightness and ease-to-handle of the FRP deck. The replacement requires only a week working period. The dead load on the bridge is reduced by 140 tons, the load rating is increased by 50%, and weight restriction can be removed.
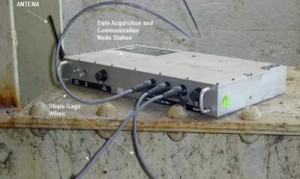
Figure 2 – Wireless Structural Monitoring System with Node Station hard-wired to the strain gages but wireless to the Base Receiver through Antenna
Load tests and structural monitoring are commonly used to gain information regarding the health and performance of an existing structure. For structures using relatively new materials, such as FRP, the use of load tests can prove the structures’ capacity. Wireless structural monitoring system is a new technology developed through a previous FHWA small business innovation research (SBIR) contract to Invocon, Inc. in Conroe, Texas. This contract developed a commercially ready data acquisition system (Figure 2) to greatly reduce the level of effort required to instrument and obtain data from bridges. The system includes a small data acquisition and communication node connected to four strain gages that can acquire data in digital form, and relay the data to a local base receiver attached to a personal computer. In this load test, five boxes were linked in a “smart” network to control the data acquisition process and find the path of least interference for data transmission. By using this system, the effort of instrumenting a bridge was reduced by more than half compared to hard-wired systems. Besides the University of Maryland, this system is also being evaluated for bridge monitoring by researchers at FHWA, Lehigh University, and the University of Texas/Austin.
The instrumentation effort, led by Drs. Fu and Amde and assisted by Ron Nelson of the FHWA and University research assistant Hamed Al-Ayed, was conducted during the week of August 27-31, 2001. Measurements were made on various elements, including FRP deck, of the bridge under live load(Figure 3). The field tests and associated finite element analyses may provide higher confidence to the owner and users in the replaced deck of the MD24 over Deer Creek Bridge and for using this new material in the future.